CLAYENS
" A World of Opportunities "
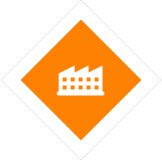
Locations
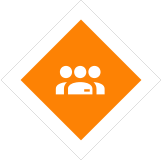
Collaborators
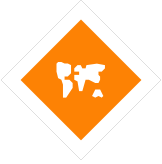
Engineering Centers
OUR CLAYENS LOCATIONS
Find us around the world
To join Clayens!
Our job offers
View all opportunities within the Group (excluding USA) and apply with just one click!
Our job offers in the USA
View all opportunities within our American subsidiaries and apply with just one click!